Featured Posts
View AllWhat is a Supply Chain Management Job and Career?
- ikram
- January 27, 2025
- 0
What is the Role of Inventory in Supply Chain Management?
- ikram
- January 13, 2025
- 0
What Makes Toyota’s Supply Chain Management a Benchmark for Excellence?
- ikram
- January 2, 2025
- 0
What is Cycle View of a Supply Chain? Is it Useful? |
- ikram
- December 12, 2024
- 6
Trending Posts
View AllWhat are The Impacts of RobotMeta on Supply Chain Management: A Case Study
- ikram
- June 5, 2025
- 0
Abstract RobotMeta is a flexible industrial robot company that specializes in welding applications. Their robots…
About the Push-Pull view of Supply Chain Process ।
- ikram
- May 25, 2025
- 4
The Supply Chain processes start cases with the express market needs, which pushes research and…
How to Explain Toyota’s Financial Management Philosophy? : A Case Study |
- ikram
- May 2, 2025
- 0
Toyota's financial management philosophy is conservative, with a low debt-to-equity ratio and a focus on…
Unveiling Amazon’s Digital Supply Chain Strategies: A Case Study
- ikram
- April 10, 2025
- 0
Abstract Amazon’s digital supply chain is a technological marvel, integrating software and hardware to…
Latest Posts
View AllWhat are The Impacts of RobotMeta on Supply Chain Management: A Case Study
- ikram
- June 5, 2025
- 0
Abstract RobotMeta is a flexible industrial robot company that specializes in welding applications. Their robots are user-friendly, allowing small and medium-sized enterprises (SMEs) to integrate robotic solutions into their operations.…
A discussion about Unilever’s Supply Chain Management : A Case Study |
- ikram
- December 2, 2024
- 0
Unilever's vast operations require a robust SCM to manage the flow of materials across continents and the company is committed to sustainable sourcing practices. Unilever's supply chain management includes advanced…
How supply chain planning works: A discussion in brief |
- ikram
- November 19, 2024
- 0
The uncertain nature of the customer demand need to take into consideration by generating the production plan and in particular the production quantities, to meet uncertain customer demand in the…
What is International export and outbound logistics of goods? |
- ikram
- November 1, 2024
- 0
In the international export trade, goods and services, i.e., international export and outbound logistics, goods and services are sold and shipped out of the jurisdiction of the country and customs…
The post Covid-19 Supply Chains: A Brief Discussion |
- ikram
- October 15, 2024
- 0
The U.S.-China trade war and the Covid-19 crisis have prompted manufacturers worldwide to reassess their supply chains, focusing on increasing domestic production, boosting employment in their home countries, reducing dependence…
Supply Chain Management
View AllWhat are The Impacts of RobotMeta on Supply Chain Management: A Case Study
- ikram
- June 5, 2025
- 0
Abstract RobotMeta is a flexible industrial robot company that specializes in welding applications. Their robots are user-friendly, allowing small and…
What is Cycle View of a Supply Chain? Is it Useful? |
- ikram
- December 12, 2024
- 6
The processes in a Supply Chain are usually divided into a series of cycles, each performed in the interface between…
How supply chain planning works: A discussion in brief |
- ikram
- November 19, 2024
- 0
The post Covid-19 Supply Chains: A Brief Discussion |
- ikram
- October 15, 2024
- 0
What are The Impacts of RobotMeta on Supply Chain Management: A Case Study
- ikram
- June 5, 2025
- 0
Abstract RobotMeta is a flexible industrial robot company that specializes in welding applications. Their robots are user-friendly, allowing small and medium-sized enterprises (SMEs) to integrate robotic solutions into their operations.…
About the Push-Pull view of Supply Chain Process ।
- ikram
- May 25, 2025
- 4
Abstract: The Supply Chain processes start cases with the express market needs, which pushes research and development, which pushes production and production pushes marketing to meet the already expressed demand.…
How to Explain Toyota’s Financial Management Philosophy? : A Case Study |
- ikram
- May 2, 2025
- 0
Abstract Toyota's financial management philosophy is conservative, with a low debt-to-equity ratio and a focus on retained earnings.The company's ambition is carefully calculated and backed by a strong equity…
Unveiling Amazon’s Digital Supply Chain Strategies: A Case Study
- ikram
- April 10, 2025
- 0
Abstract Amazon's digital supply chain is a technological marvel, integrating software and hardware to connect every link of the chain, from suppliers to customers. It uses advanced algorithms and…
What are The Impacts of RobotMeta on Supply Chain Management: A Case Study
- ikram
- June 5, 2025
- 0
Abstract RobotMeta is a flexible industrial robot company that specializes in welding applications. Their robots are user-friendly, allowing small and medium-sized enterprises (SMEs) to integrate robotic solutions into their operations.…
What is Cycle View of a Supply Chain? Is it Useful? |
- ikram
- December 12, 2024
- 6
The processes in a Supply Chain are usually divided into a series of cycles, each performed in the interface between two interrelated successive stages of a Supply Chain. Sub-processes in…
Tesla’s supply chain and logistics: A case study
- ikram
- May 1, 2023
- 0
The company was incorporated as Tesla Motors, Inc. on July 1, 2003, by Martin Eberhard and Marc Tarpenning. Eberhard verbalized he wanted to build a car manufacturer that is additionally…
H & M Supply Chain management: A case study
- ikram
- January 8, 2023
- 0
Hennes & Mauritz AB is a Swedish multinational clothing-retail company known for its fast-fashion clothing for men, women, teenagers, and children. As of November 2019, H&M operates in 74 countries…
What Makes Toyota’s Supply Chain Management a Benchmark for Excellence?
- ikram
- January 2, 2025
- 0
Toyota has an effective supply chain strategy that puts value and efficiency first. It has adopted the Just-In-Time (JIT) system, which guarantees on-demand delivery of materials and components while cutting…
Trending
View AllAbout the Push-Pull view of Supply Chain Process ।
- ikram
- May 25, 2025
- 4
Unveiling Amazon’s Digital Supply Chain Strategies: A Case Study
- ikram
- April 10, 2025
- 0
How to Explain Cold Chain as a Supply Chain and Logistical issue? |
- ikram
- March 15, 2025
- 0
Editor’s Picks
View All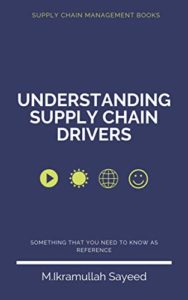
Follow Us On
Popular Posts
View AllRecent
View AllWhat are The Impacts of RobotMeta on Supply Chain Management: A Case Study
- ikram
- June 5, 2025
- 0
Abstract RobotMeta is a flexible industrial robot company that specializes in welding applications. Their robots…
About the Push-Pull view of Supply Chain Process ।
- ikram
- May 25, 2025
- 4
The Supply Chain processes start cases with the express market needs, which pushes research and…
How to Explain Toyota’s Financial Management Philosophy? : A Case Study |
- ikram
- May 2, 2025
- 0
Toyota's financial management philosophy is conservative, with a low debt-to-equity ratio and a focus on…
Unveiling Amazon’s Digital Supply Chain Strategies: A Case Study
- ikram
- April 10, 2025
- 0
Abstract Amazon’s digital supply chain is a technological marvel, integrating software and hardware to…